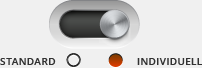
This is what we can do for you
We develop special machines for individual customer requirements and see ourselves as a customer-oriented supplier of high-grade solutions for special-purpose engineering. We implement projects from engineering right up to commissioning.
Engineering begins with the customer demand and ends with the finished CAD model, which serves as the basis for constructing the product. Engineering includes the following work steps:
- gathering customer requirements
- Consulting in automation technology, including simulations and cycle time calculations
- drafting of the specification sheet by the customer
- specification sheet / quotation by Asytec AG
- planning, development and design
- design review
- order management and manufacturing
- operating instructions in accordance with MRL 2006/42/EG with conformity assessment
After the engineering release we begin manufacturing with the production of single parts according to parts drawings. Listed below are the manufacturing options and manufacturing locations:
- In-house production of simple single parts with milling and turning machines
- Production by specialised regional suppliers
- Customer specific refinement by specialists
Components are made from single parts for a wide variety of functions and tasks. The assembly process includes the following work steps:
- component assembly and tests
- mounting of components onto modular machine frames made from aluminium strut profiles or welding and sheet metal constructions
- wiring and tubing of the components
- electric cabinet and tableau construction for electric peripherals
- attachment of the operation and visualisation modules
This milestone brings the product to life and makes it ready for preliminary acceptance after the function test. The process of commissioning is composed in the following way:
- process sequence with SPS programming
- designing and programming the HMI
- connecting databases (SQL, SAP, MES…)
- process and availability tests with specified customer parts
- testing the safety functions and safety elements
- preliminary acceptance of the customer
Welcome to Asytec AG - your expert for customized software solutions for Siemens / CoDeSys programming!
Are you looking for reliable and efficient software solutions for your Siemens or CoDeSys programming requirements? Then you've come to the right place! Asytec AG offers you customized solutions that are specifically tailored to your needs.
Our experienced team of experts has extensive know-how in the field of Siemens and CoDeSys programming and will develop innovative software solutions for you that will help you optimize your production processes and increase your efficiency.
Whether you are looking for individual control programs, visualizations or interface solutions - we have the right solution for you.
Put your trust in the many years of experience and technical expertise of Asytec AG and let our customized software solutions convince you. Contact us and find out how we can help you optimize your production processes.
After successful preliminary acceptance, the piece is transported to the customer and placed in the right spot.
- national and international delivery by post or as requested
- heavy and bulky loads are managed by us and are delivered by transport specialists
After the final assembly and connection of the media, the product will be adjusted and training provided for its upcoming task. The start-up process includes:
- provision and connection of utilities by the customer
- assembly and adjustment by our commissioning engineer on-site
- connection of prepared interfaces
- initial start-up and tests by software engineers on-site
- acceptance and test with the customer
The operating staff is trained in handling the product and prepared for potential scenarios. The training is carried out as following:
- training of the operating staff according to the operating manual
- training of the service personnel according to the maintenance plan
High availability of our products is important to us, which is why preventive measures are devised with the customer during the project phase. Our after sale service includes the following points:
- spare and wear parts list for preventive maintenance
- maintenance contract for cyclical technician assignments
- inspection assignments according to customer requirements
- our reaction time during workdays is generally less than 48 hours